EPDM
Polipropileno
Etileno Propileno Dieno Monómero Caucho (EPDM)
Los copolímeros y terpolímeros EP(D)M son elastómeros amorfos que tienen cadenas principales saturadas y, en el caso de los terpolímeros, cantidades controladas de insaturación externas a la cadena principal. EPDM es un terpolímero basado en tres monómeros: etileno, propileno y un dieno no conjugado (ethylidene norbornene ENB). Los grados de EPDM tienen una insaturación residual en las cadenas laterales y, por lo tanto, pueden curarse con azufre y aceleradores. Su resistencia al calor es claramente mejor que el caucho natural, SBR y caucho de butadieno. EPM representa un copolímero de etileno y propileno monómeros. EPM está completamente saturado y por lo tanto requiere vulcanización por radiación o productos que liberan radicales libres, como los peróxidos orgánicos. Las moléculas tanto de EPM como de EPDM tienen un hueso de hidrocarburo completamente saturado, que es excelente resistencia al calor y se logra la oxidación.
Nombres - Símbolo
- EPDM
- EPM
- Goma olefinica
- Elastómeros olefinico
- Caucho etileno-propileno
- ASTM D 1418 Designación: EPDM
- ISO/DIN 1629 Designación: EPDM
- SAE J200 / ASTM D 2000 : EPDM RUBBER AA , BA, CA, DA
Caracteristicas del caucho
Tienen la densidad más baja (0.86 g/cm3) de todas las cauchos disponibles comercialmente
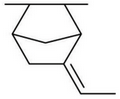
- Puede ser moldeado, extruido o calandrado
- Excelentes propiedades dieléctricas
- Capacidad para aceptar cargas de relleno más altas que otros elastómeros
- Muy buena resistencia al calor y oxidación
- Muy buena resistencia al ozono y a la intemperie
- Buena resistencia quimica
- Buena flexibilidad a baja temperatura (dependiendo del contenido de etileno)
- Buenas propiedades de aislamiento eléctrico
- Buenas propiedades físicas vulcanizadas
- Buenas comportamiento estrés-deformación, conjunto de compresión
- Bajos valores fijos permanentes
- Excelentes propiedades mecánicas y elásticas duraderas
- Flexibilidad hasta -55°C
Catalizadores
En la industria de la poliolefina, en particular para el polietileno y el polipropileno, los catalizadores Ziegler Natta (ZN) a base de titanio que se utilizan actualmente ya han estado en funcionamiento durante décadas. Estos catalizadores son muy productivos y no requieren ninguna etapa de eliminación del catalizador. El principal impulsor para desarrollar e introducir catalizadores de (post) metaloceno en la industria de la poliolefina ha sido la diferenciación del producto, lo que resulta, entre otros, en polipropileno sindiotáctico, polietileno lineal homogéneo de baja densidad y copolímeros de etileno con alfaolefina superior (plastómeros). Los polímeros de etileno, propileno y un dieno no conjugado (EPDM) representan una clase importante de elastómeros. El esqueleto de polímero completamente saturado proporciona una excelente resistencia contra el oxígeno, el ozono y el calor. El caucho EPDM se produce comercialmente utilizando catalizadores homogéneos, a saber, catalizadores de ZN a base de vanadio o, más recientemente, catalizadores homogéneos, altamente activos, bien definidos, tales como metalocenos clásicos y otros catalizadores avanzados post-metaloceno.
Los catalizadores de ZN a base de vanadio para EPDM tienen una productividad relativamente baja y, por lo tanto, deben usarse altos niveles de catalizador y generalmente se requiere la eliminación del catalizador. Los catalizadores de ZN a base de vanadio para EPDM tienen una productividad relativamente baja y, por lo tanto, deben usarse altos niveles de catalizador y generalmente se requiere la eliminación del catalizador. Sin embargo, se aplican comercialmente, porque los productos de EPDM resultantes combinan una alta carga total de compuesto con un procesamiento sencillo del compuesto y excelentes propiedades de vulcanizado. Este es el resultado directo de la microestructura óptima e intramolecular bien definida de las cadenas de polímero EPDM, a saber, una incorporación muy homogénea de los monómeros y la posibilidad de incorporar ramificaciones de cadena larga (LCB) de manera controlada.
Es bastante difícil lograr el mismo rendimiento de producto similar a ZN excelente con nuevos catalizadores. Además, como lo demuestran las carteras limitadas de EPDM basadas en catalizadores de (post-) metaloceno, hasta hace poco, aparentemente ha sido un desafío para la industria cubrir toda la pizarra de grado EPDM con catalizadores de (post) metaloceno. Casi ningún producto de EPDM con alto contenido de ENB y/o grados (de aceite extendido) de alto peso molecular basados en catalizadores de (post) metaloceno están disponibles comercialmente. Además, la introducción de un grado significativo de LCB resultó ser difícil en EPDM comerciales (post) basados en metaloceno. Para lograr buen comportamiento de procesamiento, se han propuesto estrategias de mezcla de polímeros de EPDM, pero la mezcla de polímeros siempre implicará una compensación entre el procesamiento de compuestos y el rendimiento de vulcanizado.
El nuevo sistema de catalizador tiene una estabilidad al calor sustancialmente mejorada, lo que permite temperaturas de reactor más altas y, como resultado, se requiere menos enfriamiento profundo de la alimentación de monómero. La muy alta productividad del catalizador permite la eliminación del paso de eliminación del catalizador. El sistema de catalizador de metaloceno permite la producción de una cartera completa de grado EPDM con productos que funcionan de manera idéntica a los grados EPDM, producidos por catalizadores ZN, pero con un impacto ambiental reducido. Esta cartera de EPDM cubre la más amplia gama de composición de monómeros y peso molecular. Incluye grados ENB muy altos y grados (de aceite extendido) de muy alto peso molecular. Además, la tecnología de catalizador de metaloceno crea oportunidades para desarrollar productos que no son alcanzables con Ziegler-Natta clásico o tecnologías de catalizador de metaloceno de última generación, como EPDM de alto peso molecular alto-5-vinil-2-norborneno. Los polímeros EPDM producidos con las tecnologías catalíticas más avanzadas (metaloceno) tienen varias limitaciones, es decir, las viscosidades de Mooney (ML [1 + 4] 125 ° C) están restringidas al rango de ~20-80 y el contenido de ENB generalmente es inferior a 7 peso %. La tecnología metalocénica es capaz de producir polímeros con características poliméricas idénticas a sus contrapartes Ziegler Natta y en consecuencia, propiedades idénticas de compuesto y vulcanizado. Por lo tanto, estos polímeros pueden considerarse como realmente similares. Recientemente, una nueva patente permite la fabricación de una gama completa de productos de EPDM, incluidos los polímeros de alto peso molecular (extendidos en aceite) y los polímeros con un contenido de ENB muy alto (hasta 9% en peso).
Propiedades Físico-Mecánicas
Las propiedades están directamente relacionadas con las condiciones de polimerización. Al variar los parámetros de reacción, se puede obtener una amplia gama de propiedades. La producción de una amplia gama de calidades de caucho sintético de este tipo es posible mediante una comprensión profunda de la relación entre las variables de proceso y las propiedades del producto resultante.
Influencia de la relación etileno / propileno
Si los contenidos de etileno y propileno son aproximadamente 50/50%, ambos monómeros dentro de la molécula de polímero están distribuidos uniformemente, lo que significa que el caucho es amorfo. Si el contenido de etileno es superior al 64% en peso, se forman secuencias en número y longitud crecientes, estas secuencias forman cristalitos.
En el vulcanizado, la cristalinidad del polímero mejora la resistencia a la tracción y aumenta la dureza, también mejora el compresión set a bajas temperaturas, la buena extrudabilidad y mejora la capacidad de carga de relleno y plastificante.
Caucho propiedades Termicas
El rango de temperatura de servicio continuo típico es de -50°C a 150°C. Resistencias al agrietamiento por calor a temperaturas de 130°C pueden ser obtenidas mediante sistemas de vulcanización con azufre y resistencias al calor de hasta 160°C pueden obtenerse mediante cura con sistemas de peróxido. El grado de resistencia a la oxidación bajo envejecimiento por calor está influenciado positivamente por:
• alto peso molecular
• alto contenido de etileno
Las propiedades físicas después del envejecimiento también dependen del MWD (cuanto más estrecho sea el MWD, mejor será la resistencia al calor). Debe señalarse que a altas temperaturas, los copolímeros funcionan mejor que los terpolímeros incluso si este último se cura con peróxido. El EPDM curado con azufre y aceleradores tiene menores propiedades de envejecimiento por calor.
Resistencia a baja temperatura
Los dos cambios fundamentales que tienen lugar en un elastómero cuando se baja la temperatura (endurecimiento y cristalización o parcial) parecen depender de los siguientes parámetros moleculares estructurales:
• MWD
• relación propileno / etileno
• distribución de la composición (CD)
Cuanto más estrechos sean el MWD y el CD y mayor sea el contenido de propileno, mejores serán las propiedades a baja temperatura. La presencia de un tercer monómero puede mejorar aún más las propiedades elásticas a baja temperatura.
Caucho propiedades Eléctricas
Las goma EP son normalmente buenos aislantes con una relativa alta resistividad eléctrica, siendo los no polares mejores que los polares. Sin embargo, las propiedades eléctricas de los compuestos son más dependientes de los ingredientes utilizado en la mecla que del elastómero base. Excelentes propiedades de aislamiento para el rango de baja / media tensión.
Caucho propiedades Químicas
Una de las características más importantes de los compuestos adecuadamente formulados basados en EP es su resistencia excepcional a el envejecimiento, la intemperie, oxígeno, ozono, agua, temperaturas elevadas, y radiación UV hasta cierto punto. Al ser un caucho de hidrocarburo puro, el EP también es inerte para muchos productos químicos. Su resistencia a los disolventes depende de su polaridad. La naturaleza no polar e inerte de los grados EPDM hace que los vulcanizados sean substancialmente resistentes a muchos medios polares o sustancias que contienen oxígeno en la molécula, como alcoholes, cetonas, ésteres y glicoles, y también a agua, refrigerantes típicos y líquidos de frenos, menor resistencia a la mayoría de los aceites, gasolina, queroseno, hidrocarburos aromáticos, alifáticos, disolventes halogenados, ácidos concentrados
Los polímeros también son resistentes a ácidos y bases. El EPDM generalmente tiene poca resistencia a los aceites basados en hidrocarburos y a los combustibles. Sin embargo, se puede obtener una resistencia media al aceite con los grados extendidos de aceite de peso molecular muy alto. Los altos contenidos de termonómeros mejoran la resistencia del aceite al permitir mayores densidades de reticulación.
- Agua: Excelente
- Aceites: No resiste
- Ácidos: Excelente
- Bases: Excelente
- Ozono: Excelente
- Gasolina: Pobre
Resistencia al aceite
Los cauchos de etileno-propileno tienen poca resistencia a los hidrocarburos, solventes y aceites minerales, comparables a los de los productos curados a base de SBRNR o IIR. A pesar de esto, la selección adecuada de polímeros e ingredientes compuestos le dará a los productos curados EPDM una resistencia moderada al aceite. Como regla general, las siguientes propiedades del polímero afectan la resistencia al aceite:
• peso molecular
• MWD
• contenido de etileno
Alta viscosidad Mooney, MWD estrecho y etileno medio-alto se deben seleccionar los grados de contenido EPDM. Todas estas características permiten un aumento en el estado de curado tanto en azufre/aceleración como en elementos curados con peróxido, resistiendo así la penetración de aceite en la red de polímeros.
Plastificantes
En el caso de compuestos a base de EPDM sulfurados, ambos se pueden utilizar aceites parafínicos y naftenicos. Debido a su baja volatilidad, se recomiendan aceites altamente parafínicos cuando se requiere una buena resistencia al calor. Los compuestos a base de EPDM curados con peróxido deben formularse utilizando aceite de polialquilbenceno parafínico o ramificado. Este último minimiza la interferencia con los peróxidos, lo que permite una mejor densidad de reticulación (mayor estado de curado) que el aceite parafínico.
Caucho procesabilidad
Los dos métodos de transformación más importantes para los EPDM son extrusión y calandrado. El moldeado por compresión no suele utilizarse.
Como se obtiene el caucho sintetico
Terpolímeros EPDM
Para producir un caucho curable con azufre, se introduce un dieno no conjugado como el tercer monómero durante la polimerización. Los terceros monómeros apropiados contienen un doble enlace que participa en la polimerización y otro que no. Estos resultados están en contraste con la insaturación que sirve como sitios de reticulación sin afectar la cadena principal saturada. Los terpolímeros de EPDM utilizan etilideno norborneno (ENB) como tercer monómero.
Copolímeros EPM
Los copolímeros EPM se producen por copolimerización de etileno y propileno utilizando catalizadores Ziegler Natta que se forman in situ por reacción de sales de vanadio y haluros de alquil aluminio.
En niveles altos de propileno (por encima del 50 por ciento en peso), solo corto existen secuencias de etileno en la cadena del polímero y la cristalinidad es ausente. A niveles bajos de propileno (por ejemplo, por debajo del 35 por ciento en peso), una pequeña hay una cantidad de cristalinidad presente que proporciona al EPM fuerza verde
Vulcanización EPM copolímeros
La copolimerización da como resultado un esqueleto saturado. En el caso de los copolímeros, la naturaleza saturada de la cadena polimérica no permite el curado con sistemas basados en azufre / aceleradores. Por lo tanto, se debe utilizarse curado con peróxido. El curado con peróxido de EPM es más eficiente en composiciones con alto contenido de etileno, dos para ser una escisión de cadena competitiva que se produce en los átomos de carbono terciarios de las unidades de propileno.
Vulcanización EPDM terpolímeros
Los terpolímeros se pueden reticular tanto con peróxidos como con azufre. La tasa de curación y el entrecruzamiento de los terpolímeros con altos niveles de ENB son particularmente adecuados para la producción de perfiles por presión continua.
Curado con peróxido
Tanto EPM como EPDM pueden vulcanizarse con peróxidos orgánicos. La elección del peróxido y el coagente es importante para lograr la tasa óptima de curado para las condiciones de procesamiento. La cantidad de peróxido tiene poca influencia en la velocidad de curado pero influirá en la densidad de reticulación final. Los peróxidos dan los enlaces cruzados más estables al calor. Una proporción bastante alta de etileno / propileno en el polímero contribuye a la eficiencia de reticulación. Cuando los radicales libres formados por el peróxido atacan una unidad de propileno, hay una tendencia mucho mayor a romper la cadena que a formar enlaces cruzados. Por lo tanto, se forman más enlaces cruzados por mol de peróxido en un EPDM con alto contenido de etileno que en un EPDM con bajo contenido de etileno.
Cura de azufre
Para el curado con azufre, la cantidad de termonómero en el polímero EPDM (insaturación en la cadena lateral) determina la velocidad de reticulación. Sin embargo, incluso a niveles altos de termonómeros, la EPDM tiene una reactividad más baja en comparación con el caucho natural o el caucho de butadieno, y por lo tanto, se deben usar aceleradores para lograr tiempos de curado que sean aceptables en la práctica. Se debe tener cuidado al diseñar el paquete del acelerador, ya que muchos tienen una solubilidad limitada en el EPDM, lo que puede resultar en un florecimiento de la superficie.
Relenos
Copolímeros y terpolímeros, como todos los elastómeros que no son cristalinizables bajo tensión, requieren la adición de agentes de refuerzo para adquirir altas propiedades mecánicas y elásticas. Estas propiedades se logran fácilmente agregando cargas de refuerzo comunes: negro de humo, sílice, silicatos, carbonatos de calcio, etc. Los negros de humo de hornos como FEF, APF, SRF se usan ampliamente en la producción de artículos extruidos, mientras que los tipos HAF, ISAF y GPF se usan normalmente para preparar compuestos para artículos moldeados. Los rellenos minerales generalmente dan un refuerzo más bajo que los negros de humo, dependiendo de la composición y el área de superficie.
Se pueden seleccionar de acuerdo con las propiedades deseadas sin curar y curadas. Los rellenos de naturaleza ácida (sílice, negro de carbón del canal) interfieren con los peróxidos: en este caso, el compuesto debe neutralizarse con pequeñas cantidades de óxidos metálicos (ZnO, MgO) o con aminas aromáticas (DPG). Cuando se usan azufre y aceleradores, para evitar que los rellenos altamente reforzantes adsorban los curativos, se incluyen aditivos polares, como los glicoles, en la formulación para desactivar el relleno.
Aplicaciones del caucho
El caucho EP(D)M es usado en una amplia variedad de rangos de aplicaciones desde mangueras para radiadores automotrices, cintas de empaque para ventanas, membranas de cubiertas y aislamiento de cables. También se utiliza como modificador modificador de impacto en plásticos, vulcanizado de termoplásticos TPV y aditivos para aceite de motor. La versatilidad en el diseño y performance del polímero ha resultado en el amplio uso en juntas de hermeticidad para autos, burletes para vidrio, mangueras para jardín y riego, tubos, cinturones, aislante eléctrico, membranas para techos.
Espectrometría infrarroja por Transformadas de Fourier (FTIR)
Etileno Propileno Rubber (EPR)
El catalizador Ziegler-Natta permite polimerizar a-olefinas en elastómeros con un grado controlado de cristalinidad y similitud cruzada. Los primeros EPR se fabricaron en 1960, 3 años después, el primer EPDM. Es ventajoso producir copolímeros de bloque siendo PP el bloque rígido y PE el bloque blando. Una polimerización secuencial directa de propileno y mezcla de etileno-propileno conduce a las mezclas del reactor (R-TPO). El EPR puede reticularse por peróxidos, mientras que el EPDM puede ser reticulado por los métodos estándar de la industria del caucho. Variando la composición y las variables del proceso, se puede obtener una amplia gama de propiedades. La resina con fase dispersa vulcanizada tiene CUT 125 C, superior a la TPO estándar, y se conocen como vulcanizados termoplásticos, TPV. Los grandes productores de resina, así como las casas de compuestos, fabrican diversas OPT con propiedades que van desde flexibles a rígidas (pero resistentes). El politransoctanámero (PTO) se ha utilizado como elastómero de alto rendimiento y en mezclas con resinas de ingeniería y de materias primas. Las mezclas de polioctadeceno (POD) con PP son termocrómicas. Las más interesantes son las poliolefinas policíclicas de tipo metaloceno, por ejemplo, policiclopenteno o polinorborneno, sindiotácticas o isotácticas. Los cauchos y elastómeros de etileno-propileno (también llamados EPDM y EPM) continúan siendo uno de los cauchos sintéticos más utilizados y de más rápido crecimiento con aplicaciones especiales y de uso general. Las tecnologías de polimerización y catalizadores que se utilizan hoy en día brindan la capacidad de diseñar polímeros para satisfacer las necesidades de procesamiento y aplicación específicas y exigentes. La versatilidad en el diseño y el rendimiento de polímeros ha dado como resultado un amplio uso en burletes y sellos automotrices, canales de vidrio, radiadores, mangueras de jardín y electrodomésticos, tuberías, correas, aislamiento eléctrico, membranas para techos, productos mecánicos de caucho, modificación de impacto de plástico, termoplástico vulcanizados y aplicaciones de aditivos de aceite de motor. Los cauchos de etileno-propileno son valiosos por su excelente resistencia al calor, la oxidación, el ozono y el envejecimiento debido a su estructura de cadena principal de polímero saturado y estable. Los compuestos negros y no negros debidamente pigmentados son estables al color. Como elastómeros no polares, tienen buena resistividad eléctrica, así como resistencia a disolventes polares, como agua, ácidos, álcalis, ésteres de fosfato y muchas cetonas y alcoholes. Los grados amorfos o poco cristalinos tienen una excelente flexibilidad a baja temperatura con puntos de transición vítrea de aproximadamente menos 60°C. Se puede obtener una resistencia al envejecimiento por calor de hasta 130°C con sistemas de aceleración de azufre seleccionados adecuadamente y se puede obtener una resistencia al calor a 160°C con compuestos curados con peróxido. La resistencia al endurecimiento por compresión es buena, particularmente a altas temperaturas, si se utilizan sistemas de curado con peróxido o donantes de azufre. Estos polímeros responden bien a una alta carga de relleno y plastificante, proporcionando compuestos económicos. Pueden desarrollar propiedades de alta tensión y desgarro, excelente resistencia a la abrasión, así como una mejor resistencia al hinchamiento del aceite y retardo de llama.
Procesos químicos y de fabricación
Los cauchos de etileno-propileno utilizan los mismos componentes químicos o monómeros que los polímeros termoplásticos de polietileno (PE) y polipropileno (PP). Estos monómeros de etileno (C2) y propileno (C3) se combinan de forma aleatoria para producir polímeros gomosos y estables. Se puede producir una amplia familia de elastómeros de etileno-propileno que varían desde estructuras amorfas, no cristalinas hasta semicristalinas, dependiendo de la composición del polímero y de cómo se combinan los monómeros. Estos polímeros también se producen en una gama excepcionalmente amplia de viscosidades Mooney (o pesos moleculares). Los monómeros de etileno y propileno se combinan para formar una estructura polimérica estable y químicamente saturada que proporciona un excelente calor, oxidación, ozono y envejecimiento por la intemperie. Un tercer monómero de dieno no conjugado se puede terpolimerizar de manera controlada para mantener una cadena principal saturada y colocar la insaturación reactiva en una cadena lateral disponible para la vulcanización o la química de modificación del polímero. Los terpolímeros se denominan EPDM (o etilenpropilen-dieno con "M" se refiere a la estructura de la cadena principal saturada). En la Figura 1 se ilustra una estructura de polímero de EPDM. Los copolímeros de etileno-propileno se denominan EPM.
Los dos termonómeros de dieno más utilizados son principalmente etiliden norborneno (ENB) seguido por diciclopentadieno (DCPD). Cada dieno se incorpora con una tendencia diferente a introducir ramificaciones de cadena larga (LCB) o cadenas laterales de polímero que influyen en el procesamiento y las tasas de vulcanización mediante curaciones con azufre o peróxido. Se utilizan catalizadores especializados para polimerizar los monómeros en estructuras poliméricas controladas. Desde su introducción, los elastómeros de etileno-propileno han utilizado una familia de catalizadores denominada Zeigler-Natta que lleva el nombre de sus desarrolladores iniciales. Las mejoras en los catalizadores y procesos han proporcionado una mayor productividad mientras se mantiene el control de la estructura del polímero. Más recientemente, se ha desarrollado una nueva familia de catalizadores, denominados catalizadores de metaloceno, que se encuentran en uso comercial. Hay tres procesos comerciales principales, solución, lechada (suspensión) y fase gaseosa, para la fabricación de cauchos de etilenopropileno. Los sistemas de fabricación varían con cada uno de los distintos productores. Existen diferencias en las pizarras de grado de producto fabricadas por cada productor y proceso, pero todos son capaces de producir una variedad de polímeros EPDM y EPM. Las formas físicas van desde pacas sólidas a friables, gránulos y formas granulares y mezclas de aceites. El proceso de polimerización en solución es el más utilizado y es muy versátil para fabricar una amplia gama de polímeros. Los sistemas de etileno, propileno y catalizador se polimerizan en un exceso de disolvente hidrocarbonado. Los estabilizadores y aceites, si se usan, se agregan directamente después de la polimerización. A continuación, el disolvente y los monómeros sin reaccionar se eliminan rápidamente con agua caliente o vapor, o con desvolatilización mecánica. El polímero, que se encuentra en forma de miga, se seca con deshidratación en pantallas, prensas mecánicas u hornos de secado. La miga se forma en fardos envueltos o se extruye en gránulos. Los polímeros cristalinos de alta viscosidad se venden en balas friables, compactadas libremente o como gránulos. Los grados de polímeros amorfos se encuentran típicamente en balas sólidas. El proceso de lechada (o suspensión) es una modificación de la polimerización en masa. Los monómeros y el sistema catalizador se inyectan en el reactor lleno de propileno. La polimerización tiene lugar de inmediato, formando grumos de polímero que no son solubles en el propileno. La polimerización de la suspensión reduce la necesidad de utilizar solventes y equipos de manipulación de solventes, y la baja viscosidad de la suspensión ayuda a controlar la temperatura y manipular el producto. El proceso no está limitado por la viscosidad de la solución, por lo que se puede producir un polímero de alto peso molecular sin una penalización de producción. La purga del propileno y el termonómero completa el proceso antes de la formación y el envasado. La tecnología de polimerización en fase gaseosa se desarrolló recientemente para la fabricación de cauchos de etileno-propileno. El reactor consta de un lecho fluidizado vertical. Los monómeros y nitrógeno en forma de gas junto con el catalizador se alimentan al reactor y el producto sólido se elimina periódicamente. El calor de reacción se elimina mediante el uso del gas circulante que también sirve para fluidizar el lecho de polímero. Los solventes no se utilizan eliminando la necesidad de remover, lavar y secar el solvente. El proceso tampoco está limitado por la viscosidad de la solución, por lo que se puede producir un polímero de alto peso molecular sin penalizar la productividad. Es necesaria la inyección continua de una cantidad sustancial de negro de humo utilizado como coadyuvante de partición para evitar que los gránulos de polímero se peguen entre sí y a las paredes del reactor. Los productos se fabrican en forma granular para permitir una mezcla rápida.
Los elastómeros de etileno-propileno son uno de los polímeros de caucho sintético más versátiles, de más rápido crecimiento e interesantes. Se espera que la excelente resistencia al calor, la oxidación, el ozono y el envejecimiento atmosférico proporcione un valor continuo en las exigentes aplicaciones de artículos mecánicos, de construcción y automotrices. Las tecnologías de catalizador y polimerización avanzadas actuales y emergentes también brindan la capacidad de diseñar polímeros para satisfacer las necesidades de aplicación y procesamiento que son importantes para satisfacer las crecientes demandas de calidad, uniformidad y rendimiento del producto.