Catálogo > ► Compuestos en granulos > ► Grados de poliamidas 6

Configuración del proceso de moldeo por inyección de plástico PA6
- La temperatura entre paréntesis se recomienda como valor básico establecido, la utilización de la carrera es del 35 % y 65 %, y la relación entre la longitud del flujo del módulo y el espesor de la pared es de 50:1 a 100:1.
- La temperatura de la zona de alimentación y de la zona 1 afecta directamente la eficiencia de la alimentación; aumentar estas temperaturas puede hacer que la alimentación sea más uniforme.
Temperatura sugerida del barril:
Área de alimentación 60~90°C (70°C)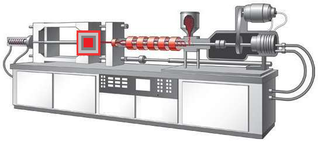
Zona 1 230 a 240°C (240°C)
Zona 2 230 a 240°C (240°C)
Zona 3 240 ~ 250°C (250°C)
Zona 4 240 ~ 250°C (250°C)
Zona 5 240 ~ 250°C (250°C)
Boquilla 230 ~ 240°C (250°C)
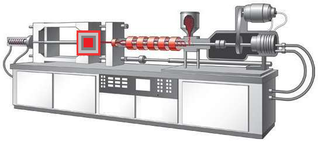
Zona 1 230 a 240°C (240°C)
Zona 2 230 a 240°C (240°C)
Zona 3 240 ~ 250°C (250°C)
Zona 4 240 ~ 250°C (250°C)
Zona 5 240 ~ 250°C (250°C)
Boquilla 230 ~ 240°C (250°C)
Temperatura de fusión: 240 ~ 250°C
Temperatura constante del barril: 220°C
Temperatura del molde: 60 ~ 100°C
Presión de inyección: 100 ~ 160 MPa (1000 ~ 1600 bar), si está procesando productos de canal largo de sección delgada (como bridas de alambre), debe alcanzar 180 MPa (1800 bar)
Presión de retención: 50 % de la presión de inyección; debido a la condensación relativamente rápida del material, un tiempo de retención corto es suficiente. Reduzca la presión para reducir la tensión en el producto.
Contrapresión: 2~8MPa (20~80bar), debe ajustarse con precisión, porque si la contrapresión es demasiado alta, provocará una plastificación desigual.
Velocidad de inyección: Se recomienda utilizar una velocidad de inyección relativamente rápida; el molde tiene buena ventilación o el fenómeno de coquización es fácil en el producto.
Velocidad del tornillo: alta velocidad del tornillo, la velocidad de la línea es de 1 m/s; sin embargo, es mejor establecer la velocidad del tornillo en un punto más bajo, siempre que el proceso de plastificación pueda completarse antes del final del tiempo de enfriamiento; se requiere un torque de tornillo más bajo
Recorrido de medición: 0,5 ~ 3,5D
Secado: secado a 80°C durante 4 h, excepto que se alimente directamente desde el recipiente de carga; el nailon absorbe el agua y debe almacenarse en un recipiente a prueba de humedad y en una tolva cerrada; un contenido de agua de más de 0,25% provocará un cambio de moldeo.
Tasa de recuperación: se puede agregar un 10% de material de retorno
Contracción: 0,7% a 2,0%; o 30% de fibra de vidrio, la contracción es de 0,3% a 0,8%; si la temperatura es más de 60 °C, el producto debe enfriarse gradualmente; el enfriamiento gradual puede reducir la contracción después del moldeo, es decir, el producto exhibe una mejor estabilidad dimensional y una pequeña tensión interna; se recomienda el método de vapor; los productos de nailon pueden inspeccionarse con fluido de soldadura
Sistema de compuerta: se pueden utilizar tipo de punto, tipo latente, tipo chip y bebedero; se recomiendan orificios ciegos y zócalos de compuerta para romper el punto frío; se puede utilizar canal caliente; debido a que la masa fundida se puede procesar en un rango de temperatura estrecho, el canal caliente debe proporcionar un control de temperatura de circuito cerrado
Tiempo de inactividad de la máquina: no es necesario limpiarla con otros materiales; la masa fundida permanece en el barril hasta 20 minutos, después de lo cual es fácil que se produzca una degradación térmica
Equipamiento del barril: tornillo estándar, alta capacidad de plastificación para geometría especial; anillo anti-retroceso, boquilla de paso recto; para la adición de refuerzo de fibra de vidrio, barril bi-metálico de alta resistencia al desgaste.
Procedimientos de puesta en marcha
- Asegúrese de que todos los calentadores estén completamente secos; no confíe en sistemas de "inicio suave" breves para lograrlo.
- Los controladores Fast Heat calientan de manera automática y segura los calentadores húmedos: solicite detalles.
- Abra las líneas de agua para establecer las temperaturas de la herramienta y del colector.
- Encienda la(s) zona(s) de control del colector y déjelas calentar hasta que el valor medido esté dentro de los 10 °C del punto de ajuste.
- Ahora encienda las zonas de punta y déjelas reposar en el punto establecido durante 5 a 10 minutos antes de comenzar la producción.
- Tome una inyección de aire desde el cañón de la máquina y verifique que la temperatura de fusión sea la correcta.
- Comience a moldear piezas en un ciclo semiautomático hasta que se establezcan los ajustes adecuados de la máquina.
- Evite retrasos prolongados entre ciclos durante este procedimiento de configuración.
- Cambie al ciclo automático cuando se estén produciendo piezas y ajuste la configuración de la máquina.
Procedimiento de apagado
La máquina y el molde se pueden apagar normalmente, sin limpiar el nailon ni del cilindro ni del canal caliente.
Al procesar material PA6, se deben considerar varios factores críticos para garantizar un rendimiento óptimo y la calidad del producto. Estos son los factores clave a tener en cuenta:
Contenido de humedad: La PA6 es higroscópica y puede absorber la humedad del ambiente, lo que puede afectar negativamente sus características de procesamiento y propiedades finales. Por lo tanto, es fundamental monitorear regularmente los niveles de humedad para mantener la integridad del material durante todo el proceso de producción.
Estabilidad térmica: El PA6 puede soportar temperaturas de hasta 310 °C sin descomponerse; sin embargo, las temperaturas de procesamiento deben mantenerse por debajo de este umbral para evitar la degradación térmica. Superar esta temperatura puede comprometer las propiedades del material, provocando decoloración y pérdida de resistencia mecánica. Un control cuidadoso de la temperatura durante el procesamiento es esencial para preservar la calidad del PA6.
Diseño del Molde: El diseño del molde desempeña un papel fundamental en el procesamiento de PA6. Factores como el tamaño de la compuerta, la ventilación y el espesor de la pared deben optimizarse para garantizar un flujo adecuado y minimizar los defectos durante el moldeo por inyección. Un molde bien diseñado facilita un flujo eficiente del material, reduce los tiempos de ciclo y mejora la calidad general de las piezas moldeadas. Una atención al diseño del molde puede influir significativamente en el éxito del proceso de moldeo por inyección.
Consideraciones sobre el reciclaje: Si se utiliza PA6 reciclado, la proporción no debe superar el 25 % del material total para mantener las propiedades mecánicas y la estabilidad del procesamiento. Además, los materiales reciclados deben secarse antes de mezclarlos con PA6 virgen para evitar problemas de humedad. El manejo y procesamiento adecuados del PA6 reciclado contribuyen a la sostenibilidad y garantizan que los productos finales cumplan con los estándares de calidad.
Tratamientos de posprocesamiento: Tras el moldeo, las piezas de PA6 pueden requerir tratamientos de posprocesamiento, como el control de la humedad, para mejorar sus propiedades mecánicas y garantizar la estabilidad dimensional. Estos tratamientos pueden incluir el recocido o condiciones de almacenamiento controladas para mitigar los efectos de la absorción de humedad. Implementar estrategias de posprocesamiento eficaces es esencial para lograr las características de rendimiento deseadas en los productos finales. Al tener en cuenta estos factores durante el procesamiento del material PA6, los fabricantes pueden optimizar sus procesos de producción y lograr resultados de alta calidad adecuados para diversas aplicaciones en las industrias de carpintería y fabricación. n diseño optimizado del molde, incluido el tamaño de la compuerta, la ventilación y el espesor de la pared, es crucial para un flujo eficiente de PA6 y para minimizar los defectos en el moldeo por inyección.
4. Conclusión
Dominar las técnicas de procesamiento del PA6 es crucial para que los fabricantes aprovechen al máximo sus excepcionales propiedades. Comprender la resistencia mecánica y la estabilidad térmica del PA6 permite a las empresas optimizar la producción para lograr eficiencia y calidad. Métodos clave como el moldeo por inyección y la extrusión son vitales para crear componentes complejos. Además, controlar el contenido de humedad y las temperaturas de procesamiento es esencial para prevenir defectos. Adoptar estas técnicas permite a los fabricantes aprovechar al máximo el potencial del PA6.
Acerca de los productos PA de Mexpolimeros
Mexpolimeros ofrece una gama de productos avanzados de PA, incluyendo compuestos de mezcla de PA6 y PA66 , diseñados para satisfacer las diversas necesidades de diversas industrias. El PA6 es conocido por su facilidad de procesamiento, baja temperatura de fusión y rentabilidad, mientras que el PA66 proporciona una resistencia superior a la temperatura, rigidez y resistencia a la abrasión. La mezcla de PA6 y PA66 combina las mejores propiedades de ambos materiales, dando como resultado un compuesto resiliente con excelentes características mecánicas. Estos compuestos se utilizan ampliamente en los sectores de la automoción y las motocicletas, y se encuentran aplicaciones en componentes como rodamientos de rodillos, carburadores y tapas de depósitos de combustible.
Los compuestos de mezcla PA6 y PA66 de Mexpolimeros están diseñados para alta precisión y resistencia, ideales para componentes de automóviles y motocicletas como cojinetes de rodillos y carburadores.
Mexpolimeros destaca por su compromiso con la calidad, ofreciendo soluciones a medida que mejoran la usabilidad y la durabilidad de los productos finales. Para las empresas que buscan compuestos plásticos fiables y avanzados, Mexpolimeros es su socio ideal. Contáctenos hoy mismo para saber más sobre cómo nuestros productos de PA pueden optimizar sus procesos de fabricación.