Catálogo > ► Compuestos virgen > ► Grados TPE-U
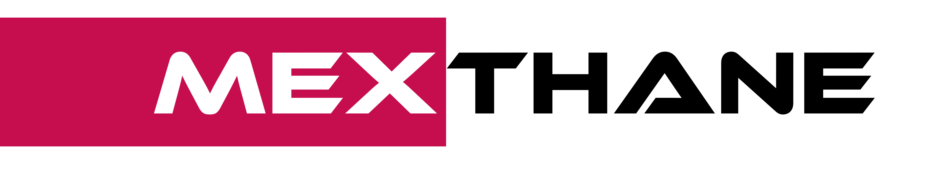

Configuración del proceso de moldeo por inyección de plástico poliuretano TPU
La dureza del TPU se suele expresar mediante la dureza Shore, reconocida internacionalmente. Generalmente, la dureza A se expresa por debajo de 100 grados, como 80A, 90A, 95A, 98A, etc., y la dureza D se expresa por encima de 100 grados, como 50D, 60D, 64D, 71D, 74D, etc. Existen diversos métodos para el moldeo de TPU, como el moldeo por inyección, el moldeo por soplado, el moldeo por compresión y el moldeo por extrusión. Entre ellos, el moldeo por inyección es el más utilizado. Su función es procesar el TPU en las piezas requeridas, que se dividen en tres procesos: preplastificación, inyección y desmoldeo. Las máquinas de inyección se dividen en dos tipos: de émbolo y de tornillo. Se recomienda utilizar máquinas de inyección de tornillo, ya que proporcionan una velocidad, plastificación y fusión uniformes. Para obtener piezas de TPU de alta calidad, se deben cumplir las siguientes condiciones relevantes durante el proceso de moldeo por inyección de plástico TPU.
Temperatura de inyección
La temperatura de inyección es uno de los factores clave que afectan la calidad de los productos de TPU, el punto de fusión del material de TPU es bajo, la temperatura de inyección es demasiado alta provocará el deterioro del material, demasiado baja provocará defectos en la superficie del producto y desviaciones dimensionales. Por lo tanto, el control de temperatura de moldeo por inyección de TPU entre 200°C ~ 240°C es más apropiado. Las temperaturas que deben controlarse en el proceso de moldeo de TPU son la temperatura del barril, la temperatura de la boquilla y la temperatura del molde. Las dos primeras afectan principalmente la plastificación y el flujo del TPU, mientras que las dos últimas afectan el flujo y el enfriamiento.
Temperatura del barril
La elección de la temperatura del barril está relacionada con la dureza del TPU. El TPU de alta dureza presenta una temperatura de fusión alta, y la temperatura máxima al final del barril también es alta. El rango de temperatura del barril utilizado para procesar TPU es de 177 a 232 °C. La distribución de la temperatura del barril generalmente va desde el lateral de la tolva (extremo trasero) hasta la boquilla (extremo delantero), aumentando gradualmente, de modo que la temperatura del TPU se eleva gradualmente para lograr una plastificación uniforme.
Temperatura de la boquilla
La temperatura de la boquilla suele ser ligeramente inferior a la temperatura máxima del cañón para evitar que el material fundido gotee en la boquilla de paso directo. Si se utilizan boquillas autoblocantes para evitar el goteo, la temperatura de la boquilla también puede controlarse dentro del rango de temperatura máxima del cañón.
Temperatura del molde
La temperatura del molde también tiene una gran influencia en la calidad de la superficie y la precisión dimensional de los productos de TPU. Una temperatura del molde demasiado alta provocará una fusión excesiva de la superficie del producto, mientras que una temperatura demasiado baja puede provocar defectos en la superficie y discrepancias dimensionales. Generalmente, una temperatura de molde adecuada para el moldeo por inyección de TPU está entre 30°C y 50°C. La temperatura del molde influye considerablemente en el rendimiento interno y la calidad aparente de los productos de TPU. Su altura depende de diversos factores, como la cristalinidad del TPU y el tamaño del producto. La temperatura del molde suele controlarse mediante un medio de refrigeración a temperatura constante, como el agua. El TPU presenta una alta dureza, alta cristalinidad y una alta temperatura de molde. Por ejemplo, Texin, con una dureza de 480A y una temperatura de molde de 20 a 30°C; dureza de 591A y una temperatura de molde de 30 a 50°C; dureza de 355D y una temperatura de molde de 40 a 65°C. La temperatura del molde para productos de TPU suele estar entre 10 y 60°C. Si la temperatura del molde es baja, la masa fundida se solidifica prematuramente, lo que produce líneas de flujo, lo que no favorece la formación de esferulitas, lo que reduce la cristalinidad del producto y provoca una cristalización posterior, lo que provoca la contracción del producto y afecta su rendimiento.
Presión de inyección
La presión de inyección es uno de los factores clave para controlar el flujo del material de TPU. Una presión de inyección demasiado alta provocará un flujo deficiente del material, burbujas, inyección insuficiente y otros defectos; una presión demasiado baja provocará defectos superficiales y desviaciones dimensionales. Como resultado, una presión de inyección adecuada para TPU está entre 50 MPa y 100 MPa. La presión de inyección incluye la presión de plastificación (contrapresión) y la presión de inyección. Cuando el tornillo retrocede, la presión sobre la masa fundida superior se denomina contrapresión, la cual se ajusta mediante una válvula de sobrepresión. Aumentar la contrapresión aumentará la temperatura de la masa fundida, reducirá la velocidad de plastificación, uniformizará la temperatura de la masa fundida, permitirá una mezcla homogénea de los materiales de color y permitirá la descarga del gas fundido, pero prolongará el ciclo de moldeo. La contrapresión del TPU suele estar entre 0,3 y 4 MPa. La presión de inyección es la presión ejercida sobre el TPU por la parte superior del tornillo. Su función es superar la resistencia al flujo del TPU desde el cilindro hasta la cavidad, llenar el molde con la masa fundida y compactarla. La resistencia al flujo del TPU y la velocidad de llenado del molde están estrechamente relacionadas con la viscosidad de la masa fundida, la cual a su vez está directamente relacionada con la dureza y la temperatura del TPU. Es decir, la viscosidad de la masa fundida no solo depende de la temperatura y la presión, sino también de la dureza y la velocidad de deformación del TPU. A mayor velocidad de cizallamiento, menor viscosidad; a velocidad de cizallamiento constante, mayor dureza del TPU, mayor viscosidad. A una velocidad de corte constante, la viscosidad disminuye al aumentar la temperatura, pero a una velocidad de corte alta, la viscosidad no se ve tan afectada por la temperatura como a una velocidad de corte baja. La presión de inyección del TPU generalmente oscila entre 20 y 110 MPa. La presión de mantenimiento es aproximadamente la mitad de la presión de inyección, y la contrapresión debe ser inferior a 1,4 MPa para que el TPU se plastifique uniformemente.
Velocidad de inyección
La velocidad de inyección es uno de los factores clave para controlar el caudal del material de TPU. Una velocidad de inyección demasiado rápida provocará un flujo desigual del material, inyecciones cortas, burbujas y otros defectos; una velocidad demasiado lenta provocará defectos en la superficie del producto y desviaciones dimensionales. Por lo tanto, el control de velocidad de moldeo por inyección de TPU entre 5 cm/s ~ 20 cm/s es más apropiado. La velocidad de inyección depende principalmente de la configuración del producto de TPU. Los productos con extremos gruesos requieren una velocidad de inyección menor, mientras que los de extremos delgados ofrecen una mayor velocidad. El procesamiento de productos de TPU suele requerir una baja velocidad de corte, por lo que es adecuada una velocidad de tornillo más baja. La velocidad del tornillo de TPU suele ser de 20 a 80 r/min, preferiblemente de 20 a 40 r/min.
Tiempo de enfriamiento
El tiempo de enfriamiento es uno de los factores clave para controlar el tamaño y la calidad de la superficie de los productos de TPU. Un tiempo de enfriamiento demasiado corto dará lugar a productos que no se curen completamente, con marcas de fusión visibles, deformaciones y otros defectos; un tiempo demasiado largo dará lugar a una extensión del ciclo del proceso y a una reducción de la productividad. En consecuencia, el tiempo de enfriamiento de los productos de TPU se controla entre 10 y 60 segundos. Para conocer valores específicos, consulte la siguiente tabla de temperaturas de procesamiento de TPU en moldeo por inyección. El tiempo necesario para completar un proceso de inyección se denomina ciclo de moldeo. Este ciclo incluye el tiempo de llenado del molde, el tiempo de mantenimiento de la presión, el tiempo de enfriamiento y otros tiempos (apertura, desmoldeo y cierre del molde, etc.), que afectan directamente la productividad laboral y la utilización del equipo. El ciclo de moldeo del TPU suele depender de la dureza, el espesor de la pieza y la configuración. Si el TPU tiene una dureza alta, el ciclo es corto; si las piezas de plástico son gruesas, el ciclo es largo; si la configuración de las piezas de plástico es compleja, el ciclo es largo. El ciclo de moldeo también depende de la temperatura del molde. El ciclo de moldeo del TPU suele durar entre 20 y 60 s.
Procedimiento de Arranque
- Asegúrese de que todos los calentadores estén completamente secos; no confíe en sistemas de arranque suave.
- Los controladores Fast Heat hornean automáticamente y de forma segura los calentadores húmedos. Solicite más información.
- Abra las tuberías de agua para estabilizar la temperatura de la herramienta y del colector.
- Abra la(s) zona(s) de control del colector y deje(n) calentar hasta que el valor medido se encuentre a 10°C del punto de ajuste.
- Ahora, abra las zonas de la punta y deje(n) asentarse en el punto de ajuste durante 5 a 10 minutos antes de iniciar la producción.
- Tome una muestra de aire del cilindro de la máquina y compruebe que la temperatura de fusión sea correcta.
- Comience a moldear las piezas en un ciclo semiautomático hasta que se establezcan los ajustes adecuados de la máquina.
- Evite largas demoras entre ciclos durante este procedimiento de ajuste.
- Cambie al ciclo automático cuando se estén produciendo las piezas y ajuste la configuración de la máquina.
Procedimiento de Apagado
La máquina y el molde pueden apagarse normalmente, sin purgar el TPU del cilindro ni del canal caliente.
Diseño de la máquina de inyección
El cilindro de la máquina de inyección está revestido con una aleación de cobre y aluminio, y el tornillo está cromado para evitar el desgaste. La relación longitud-diámetro del tornillo es preferiblemente de 16 a 20 (al menos 15); la relación de compresión es de 2,5 a 3,0. La sección de alimentación tiene una longitud de 0,5 L, la sección de compresión de 0,3 L y la sección de dosificación de 0,2 L. Se debe instalar un anillo de retención cerca de la parte superior del tornillo para evitar el reflujo y mantener la presión máxima. Para procesar TPU, se deben utilizar boquillas autofluyentes. La salida es de cono invertido y el diámetro de la boquilla es superior a 4 mm, inferior a los 0,68 mm de la entrada del canal principal. La boquilla debe estar equipada con una banda de calentamiento controlable para evitar la solidificación del material. Desde un punto de vista económico, el volumen de inyección debe ser del 40 % al 80 % del volumen nominal. La velocidad del tornillo es de 20 a 50 rpm.
Diseño de moldes
Preste atención a los siguientes puntos en el diseño del molde:
Contracción de piezas moldeadas de TPU
La contracción se ve afectada por las condiciones de moldeo, como la dureza de la materia prima, el espesor, la forma, la temperatura de moldeo y la temperatura del molde de la pieza. Normalmente, el rango de contracción es de 0,005 a 0,020 cm/cm. Por ejemplo, una probeta rectangular de 100 x 10 x 2 mm tiene una compuerta longitudinal y se contrae en la dirección del flujo; la dureza de 75A es de 2 a 3 veces mayor que la de 60D. El efecto de la dureza y el espesor del TPU en la contracción se muestra en la Figura 1. Se puede observar que, cuando la dureza del TPU está entre 78A y 90A, la contracción de la pieza disminuye al aumentar el espesor; cuando la dureza está entre 95A y 74D, la contracción aumenta ligeramente al aumentar el espesor.
Canal y cavidad fría
El canal principal es una sección del molde que conecta la boquilla de la máquina de inyección con el canal secundario o cavidad. Su diámetro debe ampliarse hacia adentro en un ángulo de más de 20° para facilitar el desmoldeo del molde. El canal secundario es el canal que conecta el canal principal con cada cavidad en un molde multiranura. Su disposición en el molde debe ser simétrica y equidistante. El canal puede ser redondo, semicircular o rectangular, con un diámetro de 6-9 mm. La superficie del canal debe pulirse como una cavidad para reducir la resistencia al flujo y acelerar el llenado. La cavidad fría es una cavidad ubicada al final del canal principal que captura el material frío generado entre dos inyecciones en el extremo de la boquilla, evitando así la obstrucción del canal o la compuerta. El material frío se mezcla en la cavidad, por lo que el producto es propenso a tensiones internas. La cavidad fría tiene un diámetro de 8 a 10 mm y una profundidad de aproximadamente 6 mm.
Puerta y salidas
La compuerta es un canal que conecta el canal principal o secundario con la cavidad. Su sección transversal suele ser menor que la del canal, que es la parte más pequeña del sistema, y su longitud debe ser corta. La compuerta puede ser rectangular o redonda, y su tamaño aumenta con el grosor del producto. El grosor del producto es inferior a 4 mm y su diámetro es de 1 mm; el grosor es de 4 a 8 mm y su diámetro es de 1,4 mm. La compuerta se coloca generalmente en la parte más gruesa del producto, sin afectar su apariencia ni su uso, en ángulo recto con la pared del molde para evitar la contracción y la formación de remolinos. El puerto de escape es una salida de aire con forma de ranura que se abre en el molde para evitar que la masa fundida que entra en el molde quede atrapada en el gas y se expulse de la cavidad. De lo contrario, el producto presentará agujeros de aire, soldadura deficiente, relleno insuficiente o incluso se quemará debido a la alta temperatura causada por la compresión del aire y la tensión interna en la pieza. El puerto de escape puede instalarse al final del flujo de masa fundida en la cavidad o en la superficie de separación del molde. Es una colada de 0,15 mm de profundidad y 6 mm de ancho. Se debe tener cuidado de controlar la temperatura del molde lo más uniformemente posible para evitar deformaciones y deformaciones de las piezas.
Estado del moldeo
Las condiciones de moldeo más importantes del TPU son la temperatura, la presión y el tiempo, que afectan el flujo y el enfriamiento de la plastificación. Estos parámetros influirán en la apariencia y el rendimiento de las piezas de TPU. Unas buenas condiciones de procesamiento permiten obtener piezas uniformes de color blanco a beige.
Detener el procesamiento
Dado que el TPU puede degradarse durante un tiempo prolongado bajo altas temperaturas, después de apagarlo, se debe limpiar con PS, PE, plástico acrílico o ABS; si se apaga durante más de 1 hora, se debe apagar la calefacción.
Post-procesamiento de productos
Debido a la plastificación desigual en el cilindro o a las diferentes velocidades de enfriamiento en la cavidad del molde, el TPU suele presentar cristalización, orientación y contracción desiguales, lo que genera tensiones internas en los productos. Esto es más evidente en productos de paredes gruesas o con insertos metálicos. Los productos con tensiones internas suelen sufrir una disminución de sus propiedades mecánicas durante el almacenamiento y el uso, presentando vetas plateadas en la superficie o incluso deformaciones y grietas. Una solución para estos problemas en la producción es el recocido. La temperatura de recocido depende de la dureza del TPU. La temperatura de recocido para productos con alta dureza también es más alta, y la temperatura para productos con baja dureza es más baja. Una temperatura demasiado alta puede causar deformaciones o deformaciones, y una temperatura demasiado baja impide eliminar las tensiones internas. El recocido del TPU debe realizarse a baja temperatura durante un tiempo prolongado, y los productos con menor dureza alcanzan su mejor rendimiento tras varias semanas a temperatura ambiente. Cuando la dureza es inferior a Shore A85, se recoce a 80°C durante 20 h, y para productos con durezas superiores a A85, a 100°C durante 20 h. El recocido se puede realizar en un horno de aire caliente, teniendo cuidado de no sobrecalentar localmente y deformar el producto. El recocido no solo elimina la tensión interna, sino que también mejora las propiedades mecánicas. Dado que el TPU es bifásico, la mezcla de fases se produce durante su procesamiento térmico. Durante el enfriamiento rápido, debido a la alta viscosidad del TPU, la separación de fases es muy lenta, por lo que se requiere tiempo suficiente para que se separen y formen microdominios para obtener un rendimiento óptimo.
Inyección de mosaico
Para satisfacer las necesidades de ensamblaje y resistencia, es necesario incrustar insertos metálicos en piezas de TPU. El inserto se coloca primero en una posición predeterminada en el molde y luego se inyecta en el producto completo. En productos de TPU con insertos, debido a la gran diferencia de rendimiento térmico y la contracción entre el inserto metálico y el TPU, la unión entre ambos no es buena. La solución es precalentar el inserto metálico, ya que reduce la diferencia de temperatura de la masa fundida después del precalentamiento, de modo que la masa fundida alrededor del inserto se enfríe lentamente durante el proceso de inyección y la contracción sea más uniforme. Se produce cierta contracción del material caliente para evitar una tensión interna excesiva alrededor del inserto. El moldeo de insertos de TPU es relativamente sencillo y su forma es ilimitada. Una vez desengrasado, el inserto se calienta a 200-230°C durante 1,5-2 minutos, y su resistencia al desprendimiento puede alcanzar de 6 a 9 kg/25 mm. Para una unión más fuerte, aplique adhesivo al inserto, caliéntelo a 120°C y luego inyéctelo. Además, cabe señalar que el TPU utilizado no debe contener lubricantes.
Reutilización de materiales reciclados
En el proceso de procesamiento de TPU, se pueden reciclar materiales de desecho como el canal principal, el canal secundario y productos de baja calidad. Según los resultados experimentales, el 100 % de los materiales reciclados no se mezclan con materiales nuevos, por lo que la disminución de las propiedades mecánicas no es grave. Se puede utilizar en su totalidad, pero para mantener las propiedades físicas y mecánicas y las condiciones de inyección óptimas, se recomienda una proporción de materiales reciclados del 25 % al 30 %. Cabe destacar que las especificaciones del material recuperado y del material nuevo deben ser, preferiblemente, las mismas. Se debe evitar el material recuperado contaminado o recocido. El material recuperado no debe almacenarse durante demasiado tiempo. Es mejor granularlo y secarlo inmediatamente. La viscosidad de fusión de los materiales reciclados generalmente se reduce y se ajustan las condiciones de moldeo.